Extend the service life of screen changer for recycling processes
The frequent blockage of screen changer for recycling processes seriously affects the normal production of Juku and downstream filament device. For this reason, combined with the actual production situation, through large factor analysis and technical improvement, the service life of the filter element is prolonged, and frequent blockage of the melt filter is avoided.
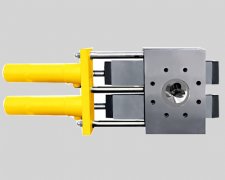
Melt filters are widely used in polyester and spinning production lines. Their main purpose is to remove solid impurities such as organic melts, carbonized particles and metal oxides in melts, improve product quality, provide qualified raw materials for downstream processes and ensure normal production of downstream processes.
After removal of the filter element of the screen changer for recycling processes, due to the residual polyester melt at the bottom of the inner tank, the inner wall and the inlet and outlet pipelines, if not removed, it is very easy to carbonize in the preheating process, blocking the melt filter when switching, greatly shortening the service life of the filter. In view of the characteristics of high temperature and narrow space of inner liner, the lower head should be dismantled every time before installation. First, it is cleaned manually, and then it is blown back by gas. The effect is very ideal. At the same time, we should pay attention to the following problems in use: if the preheating time is short, the resistance of melt passing through the filter element increases due to uneven heating during switching, and the service life of the filter element decreases. Therefore, the best preheating time should be 48 hours; the large pressure difference of the filter element should be controlled, switched in time, and the filter element should be protected, with a large pressure difference of 6.0 MPa. After each switch, close the cut filter inlet and outlet valves to avoid leakage.